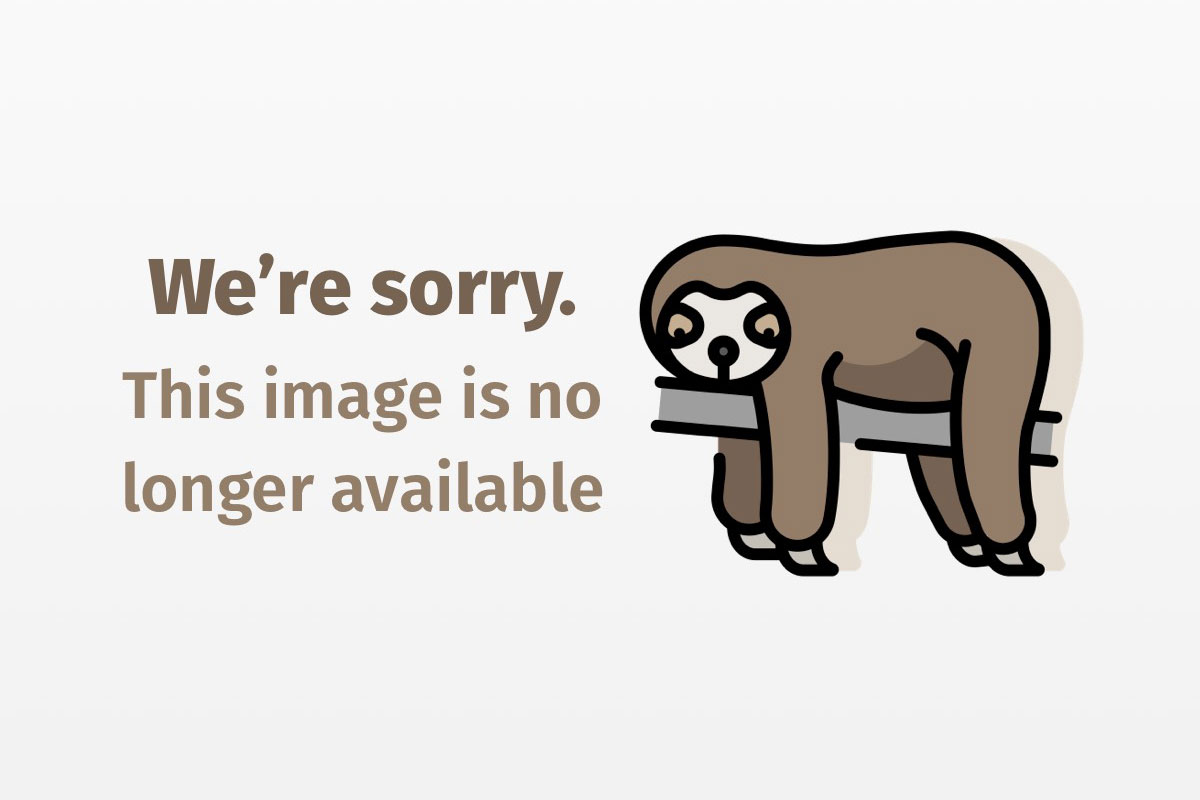
Raising the roof
CTOs in the construction industry are pushing wireless and collaboration features despite cultural and business constraints
FOR JOHN VOELLER, chief knowledge and technology officer of the worldwide construction and engineering company Black & Veatch (BV), building a major chemical or power plant involves far more than the physical act of putting bricks and mortar together.
Voeller says the Kansas City, Mo.-based company’s sophisticated collaborative software platform allows him to bring together diverse parties and data to complete complex tasks.
And by extension, BV has increased deployment of intelligent devices to track and monitor building processes. Voeller is also developing a wireless strategy to empower field workers to access needed information instantly, no matter where they are. With staff often spending months at some building sites — working from trailers without simple phone hook-ups — wireless is the ultimate solution.
“The 802 standard is the key. With 802.11 a and [802.11]b, we have something to work with on [construction] sites,” Voeller says. BV has outfitted about 15 people with wireless devices using Sprint PCS wireless cards. Plans are in place for more than 100 company supervisors to have devices within a year,” he says.
“Companies that use new technologies first in this industry are the biggest ones — such as Black & Veatch and Bechtel — that have the expertise and economies of scale,” says Scott Tiazkun, enterprise application group research manager at Framingham, Mass.-based IDC.
Voeller saw all these trends coming years ago. “But we had to stamp our feet and wait for others in the industry to catch up,” he says.
Building a wireless foundation
Smaller AEC (architecture, engineering, and construction) companies are beginning to catch up and catch on. They are, for the most part, concentrating on particular technologies that offer a clear ROI, says Laurie Balch, senior analyst for design and engineering at Stamford, Conn.-based Gartner Dataquest.
“The AEC industry is historically reticent to adopt new technology,” says Balch. “In any project, there are so many players that you find a lot of people who are small and who don’t need to use technology as some of these larger folks do.”
That move has been slow for some companies. But CTOs in the industry say they are seeking to expand wireless connectivity as a way to increase communications and efficiency, says Lowell Vice, VP and CTO of New York-based Turner Industries. Vice says about 10 upper-level managers are using BlackBerry devices and “we continue to look at wireless possibilities.”
Executives at Detroit-based SmithGroup, an architecture and design firm with 900 employees in eight offices across the country, are often traveling or at remote building sites, and as such are looking for help from collaboration software, wireless connectivity, and pen-based computing devices, says Derek White, the company’s director of IT. “That’s where we are looking to go,” White says. “The technology is starting to get to where you can get out of the office.”
SmithGroup used Metricom’s Ricochet wireless network until that company halted service and filed for bankruptcy in August 2001. Now SmithGroup is hooked up with an AT&T wireless network, including laptop and mobile connectivity. The company is adding next-generation 3G services and deploying GSM (Global Systems for Mobile communications) and GPRS (General Packet Radio Service) for faster and more varied services.
Vice and White say they see wireless communications as way to use technology at an affordable price. “As U.S. companies are building out their wireless networks, we are starting to see higher connection speeds,” White says. “We are really starting to see the benefits.”
BV’s Voeller is looking beyond standard wireless solutions to deploying RFID (Radio Frequency Identification), which uses tags to transmit wireless messages. Such a system could keep track of the thousands of pieces of equipment and materials used at construction sites, he says.
Back to the drawing board
Wireless is often the solution that is the easiest to adopt and packs an immediate punch. Still, many construction companies are overcoming constraints as they adopt technical strategies, say industry experts. Midsize companies such as SmithGroup and Turner Industries are implementing modest technology deployments that fit their size and business plan.
BV is on the front end of an industry trend. “We are seeing the beginnings of where companies say to us, ‘We don’t want you to just build the plant, but plan it, build it, and maintain it, and we’ll just buy the product,’ ” Voeller says.
It’s an alluring vision. But in reality, most construction and engineering companies lack the resources and opportunity for such grand plans. Instead, analysts say, AEC companies are concentrating on implementing more readily accessible, mainstream technologies such as collaborative CAD platforms and increasing wireless deployment.
While AEC companies look to collaboration applications as a way to streamline workflow processes among many partners in construction projects, BV developed its own computer-aided design and project management system in the 1980s and continues to extend it.
Called PowerTrak, the platform uses a relational database, including 2-D and 3-D computer-aided design models as well as construction applications such as estimating, delivery, purchasing, field management, and project control. Indicative of the breadth is the BV Solutions Group, an IT support group with a network of more than 6,000 PCs, 300 servers, 50 midrange servers, and extensive networks consisting of point-to-point, frame relay, and ISDN circuits worldwide.
Collaboration technology is used by many AEC companies to streamline collaboration, but the market is still “immature,” says Gartner Dataquest’s Balch. Added to that is the closing of several industry markets and exchanges during the dot-com bust.
SmithGroup’s White has implemented several applications from San Rafael, Calif.-based Autodesk, a leading CAD vendor along with Citadon and Bentley Systems. For example, one employee is working on-site at the University of California at San Francisco using a Compaq iPac PDA and Autodesk’s OnSite application, which gives her access to design data. “OnSite allows her to download drawings to her iPac so she can call them up in the field,” White says. SmithGroup is also using Autodesk’s AutoCAD automated design and drafting platform and Autodesk Architectural Studio, which offers collaboration tools.
White says SmithGroup’s architects and designers enjoy using the pen-based drawing features offered by Autodesk. “We’ve got some incredibly talented designers,” White explains. “But they learned to draw with a pen. So we want to use pen-based computers to do conceptual work.”
In contrast, Turner Industries has shied away from the entrenched CAD-related applications because the company’s organizational structure doesn’t lend itself to collaboration, says CTO Vice. “We looked at CAD for several areas of the company but we just haven’t seen enough return on investment.”
Each of the 15 industrial companies comprising Turner Industries “is doing something different,” Vice says. “They do some collaboration but for the most part they work independently.” Companywide, Turner uses Cognos to provide Web-based business intelligence about Turners’ operations and an ERP system from J.D Edwards, which integrates documents with an imaging management system from Image Integrated Solutions, Vice says.
At BV, Voeller sums up much of where the industry stands. His company is adopting new technologies as quickly as possible. “We are not bleeding-edge people in terms of technology development, but we’ve found that the opportunities are running so fast that it’s in our interest to follow them as much as possible.”
